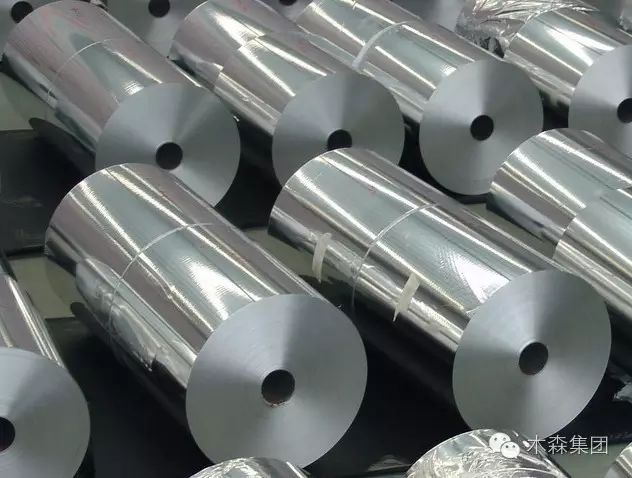
How much do you know about how to deal with defects during aluminum foil roll process(1)
Due to more production processes, more difficult processing technology and the thinnest finished product thickness of aluminum foil rolling, the probability of defects is many times higher than other pressure processing, and efforts to reduce and eliminate rolling defects is one of the keys to achieve safe, high-quality, efficient and low-consumption production. Nine defects may appear during the process are following:
No.1 Holes
The place and size of the holes on the surface of the aluminum foil are mainly concentrated in the head and tail, sometimes in the whole volume.
The main causes of holes are as follows:
a) The roll surface is damaged;
b) During the production process, cracks are formed after foreign materials fall off;
c) The surface of the incoming materials have defects such as inclusions, airways, and serious scratches;
d) Excessive reduction leads to uneven deformation;
Measure
1, The head and tail at a low speed ritual when rolling.
2, Keep the sample, measure the continuous holes in the whole volume.
3, change the roll for the roll problem.
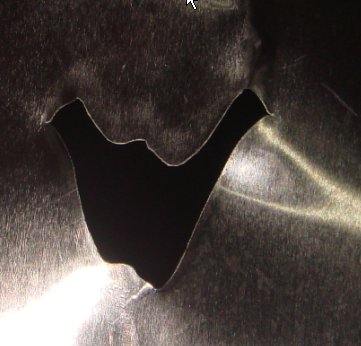
No.2 Dislocated Layer
The end face of the aluminum foil roll is irregular between the layers. The end face is uneven.
The main causes of crosstalk are as follows:
a) Uneven billet;
b) Improper reeling tension adjustment;
c) Improper adjustment of the flattened roller;
d) The alignment system is abnormal during the take-up;
e) Excessive speed when rolling or slitting;
Measure
1. Reduce the speed of production appropriately.
2. Adjust the tilt or pressure of the flattening silver during operation correctly.
3. Inform the fitter to flatten the roll.
4. Change processing parameters slowly.
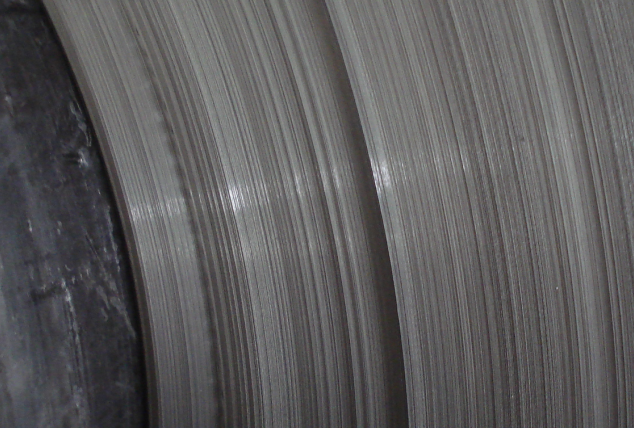
No.3 Corrosion
Foil defects produced from aluminum foil surface and the surrounding medium contact chemical reaction or electrochemical reaction, corroded aluminum foil surface will lose luster, may also produce gray corrosion products in more serious condition.
The main causes of corrosion are as follows:
a) Improper storage of aluminum foil during production and transportation, corrosion caused by humid climate or rain immersion;
b) The rolling oil contains water or is alkaline;
c) Water in high-pressure wind;
d) The anti-corrosion packaging film is damaged during storage and transportation. The blank is oxidized during transportation and storage;
e) Storage time is too long;
Measure
1, Strict inspection of the blank into the factory.
2, Keep dry, pure compressed air condition.
3, Control the moisture content of rolling oil strictly, and regularly detect.
4, Wipe the steam condensate on exit side.
5, For aluminum with water spots, low rolling speed, high load production.
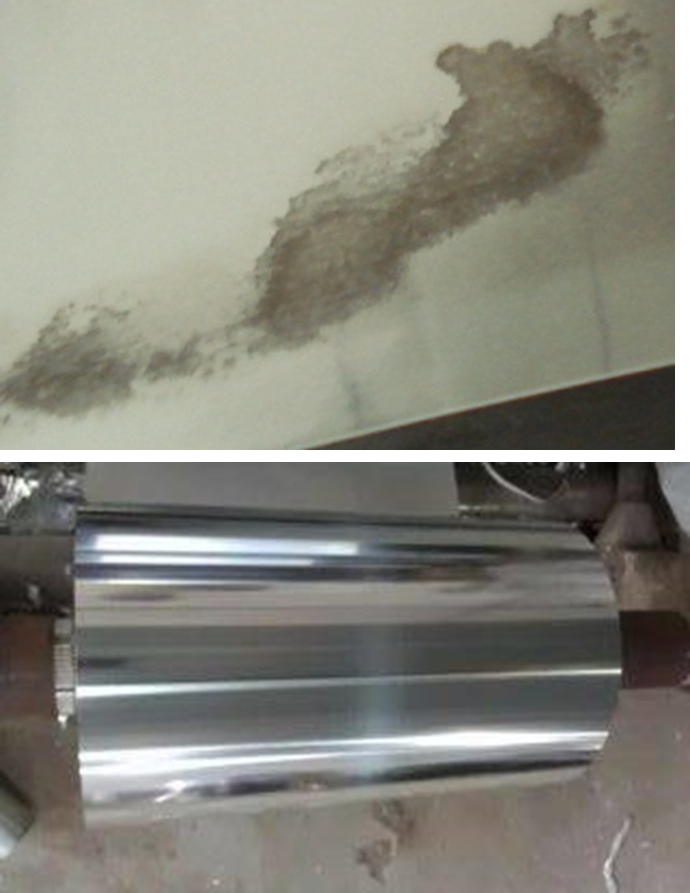
No.4 Wrinkling
Longitudinal or transverse creasing caused by the failure of the foil roll surface to flatter. It may occur when the outlet thickness of the aluminum foil is below 0.05nm and the possibility of wrinkling increases with the decrease of thickness.
The main causes of wrinkling are as follows:
a) Billet plate is in bad shape or wrinkled;
b) Improper control of Roll profile;
c) Improper control of rolling and scuttling process parameters;
d) The precision of rolling system is not enough;
e} The sleeve or core is not accurate enough;
Measure
1, Improve the level of operation, strengthen the judgment competence of the plate shape.
2,In the process range, timely adjust the rolling process parameters: strengthen cooling at the loose place, increase the front tension, etc.
3, Check for rolling oil thrown in from the back.
4, Adjust the flattening roll appropriately.
5, Consider replacing the work roller.
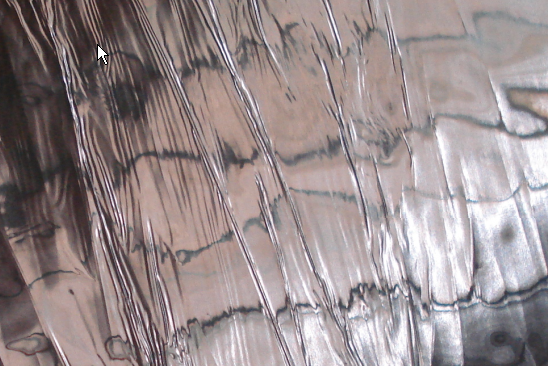
No.1 Holes
The place and size of the holes on the surface of the aluminum foil are mainly concentrated in the head and tail, sometimes in the whole volume.
The main causes of holes are as follows:
a) The roll surface is damaged;
b) During the production process, cracks are formed after foreign materials fall off;
c) The surface of the incoming materials have defects such as inclusions, airways, and serious scratches;
d) Excessive reduction leads to uneven deformation;
Measure
1, The head and tail at a low speed ritual when rolling.
2, Keep the sample, measure the continuous holes in the whole volume.
3, change the roll for the roll problem.
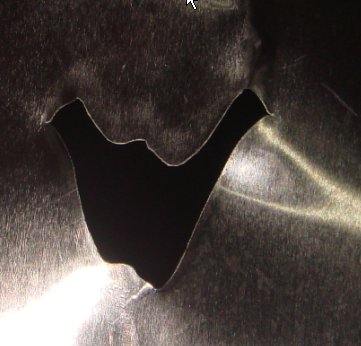
No.2 Dislocated Layer
The end face of the aluminum foil roll is irregular between the layers. The end face is uneven.
The main causes of crosstalk are as follows:
a) Uneven billet;
b) Improper reeling tension adjustment;
c) Improper adjustment of the flattened roller;
d) The alignment system is abnormal during the take-up;
e) Excessive speed when rolling or slitting;
Measure
1. Reduce the speed of production appropriately.
2. Adjust the tilt or pressure of the flattening silver during operation correctly.
3. Inform the fitter to flatten the roll.
4. Change processing parameters slowly.
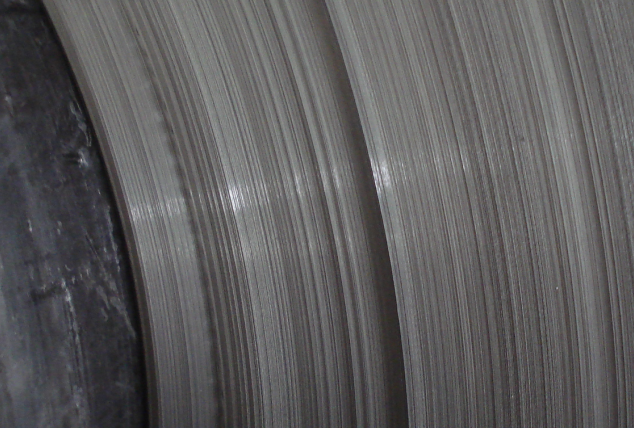
No.3 Corrosion
Foil defects produced from aluminum foil surface and the surrounding medium contact chemical reaction or electrochemical reaction, corroded aluminum foil surface will lose luster, may also produce gray corrosion products in more serious condition.
The main causes of corrosion are as follows:
a) Improper storage of aluminum foil during production and transportation, corrosion caused by humid climate or rain immersion;
b) The rolling oil contains water or is alkaline;
c) Water in high-pressure wind;
d) The anti-corrosion packaging film is damaged during storage and transportation. The blank is oxidized during transportation and storage;
e) Storage time is too long;
Measure
1, Strict inspection of the blank into the factory.
2, Keep dry, pure compressed air condition.
3, Control the moisture content of rolling oil strictly, and regularly detect.
4, Wipe the steam condensate on exit side.
5, For aluminum with water spots, low rolling speed, high load production.
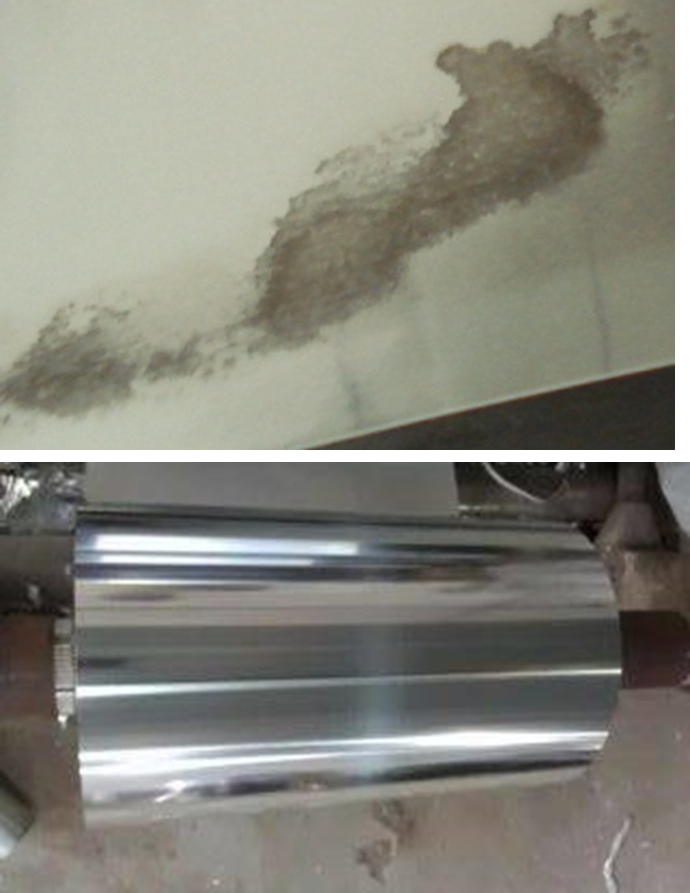
No.4 Wrinkling
Longitudinal or transverse creasing caused by the failure of the foil roll surface to flatter. It may occur when the outlet thickness of the aluminum foil is below 0.05nm and the possibility of wrinkling increases with the decrease of thickness.
The main causes of wrinkling are as follows:
a) Billet plate is in bad shape or wrinkled;
b) Improper control of Roll profile;
c) Improper control of rolling and scuttling process parameters;
d) The precision of rolling system is not enough;
e} The sleeve or core is not accurate enough;
Measure
1, Improve the level of operation, strengthen the judgment competence of the plate shape.
2,In the process range, timely adjust the rolling process parameters: strengthen cooling at the loose place, increase the front tension, etc.
3, Check for rolling oil thrown in from the back.
4, Adjust the flattening roll appropriately.
5, Consider replacing the work roller.
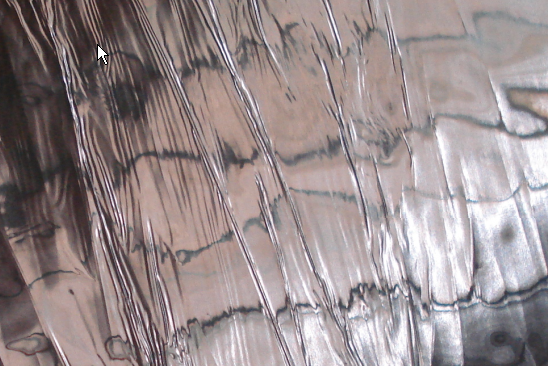